|Practical help|
Accident examples
Fatal accident on a wrapping machine
Circumstances of the accident
The employee entered the danger zone of a palletizing system to prepare new film material. He was hit by the wrapping machine and fatally injured in the head. The machine was in operation and the safety light barriers had been manipulated; the light barriers had been moved so far upwards that access below the lowest light barrier was easily possible. This meant that the drives were not shut down when the danger zone was entered.
Accident cause
The safety light barriers were manipulated in order to avoid costly troubleshooting. If the light barriers were interrupted, e.g. to refill film material, the pneumatic system vented and the clamping grippers opened. This meant that the shirred film had to be manually cut off and rethreaded. By moving the light barriers upwards, access to the danger zone was possible without the pneumatic system being vented.
Accident prevention
The accident could have been avoided because the reason for the manipulation is easy to eliminate. From a safety point of view, it is possible to configure the clamping grippers so that they do not open when the light barrier is interrupted and only the dangerous movements of the palletizing system are stopped. This change would have allowed access to the danger zone without the need for time-consuming troubleshooting.
Fatal accident on a CNC lathe
Circumstances of the accident
An experienced worker was tasked with machining a stainless-steel shaft on a CNC lathe. In the course of the work, he opened the safety guard and leaned into the machining area. He was hit by the rotating three-jaw chuck and pulled into the machine, suffering fatal injuries.
Cause of the accident
The work is performed in automatic mode. Normally, therefore, the machine operator is protected from the hazardous movements of the machine by a safety guard. For unknown reasons, however, the lathe operator had fabricated a duplicate of the interlocked guard’s mechanical actuator and plugged it into the electromechanical door switch, thereby disabling the safety guard’s protective function.
Accident prevention
To prevent the safeguard from being defeated in future, the position switch on the guard was replaced by an interlocking device with high coding level. In future, it will no longer be possible to bypass the system easily. The operator also conducted dedicated in-house instruction on proper use of the machine tools and their safeguards.
Machine operator loses entire arm on a roller infeed
Circumstances of the accident
A machine operator intended to remove debris from the toothed rollers of a carding machine. To do this, he opened the safety guard while the machine was coasting to a halt, and entered the machine’s operating area. During the cleaning process, the hose used for cleaning was caught by the clothing roller and drawn in. As the machine operator attempted to pull the air hose clear, his hand was caught in the infeed point. Owing to the high moment of inertia, the machine continued to run unchecked and pulled the operator’s left arm in as far as the shoulder.
Cause of the accident
To save time and begin clearing a fault whilst the machine was still coasting to a halt, the machine operator bypassed the guard locking device by using a special operating mode intended for maintenance purposes. Use of the special operating mode is permitted only for certain maintenance activities, for example changing of the card clothing, and only by skilled personnel trained in its use. In the company where the accident occurred, however, it had become standard practice to leave the key for selecting the operating mode permanently in the switch.
Accident prevention
The key for selecting the operating mode is to be accessible only to skilled and trained personnel. These employees must be selected carefully according to their level of qualification, and instructed regularly on hazards and alternative measures. Authorization to use the switch should be issued in writing by company management. It is recommended that the key(s) be held by a responsible person, and that release of the key(s) for switching operations be documented together with the date and the task to be performed.
A special operating mode intended only for certain tasks must not be permanently active. Measures must therefore be provided in the machine control system to detect improper continuous operation and to shut down the machine in the event of violation.
Temporary worker seriously injured on a milling machine
Circumstances of the accident
A temporary worker was tasked with machining threads in holes on a horizontal milling machine. After completing the work process, the worker entered the machining area through the safety guard to check the holes. As he was checking the thread depth by means of a test mandrel, the milling machine suddenly started up inadvertently, despite the safety guard being open. The milling machine’s spindle caught the temporary worker’s jacket and began pulling it into the machine. While attempting to free himself, the temporary worker fell so badly that he suffered severe injuries to his ribs and lung.
Cause of the accident
Since the work is performed in an automatic process, the machine operator is protected from hazardous machine movements by the interlock on the safety guard. When the guard is opened, the machine is safely brought to a halt and unexpected start-up is prevented. However, the interlocking device on the safety door had been defeated: the actuator had been unscrewed from the door of the machine for this purpose. It transpired that defeating of the safeguard had long been known in the company and was evidently also tolerated by superiors. The temporary worker himself was not aware of the tampering.
Accident prevention
During investigation of the accident, the risk assessment was revised and the machine retrofitted with position switches with high coding level to make defeating more difficult. In addition, the machine’s safety concept was revised to reduce the incentive for defeating of its safeguards.
Fatal accident on a cup filling machine
Circumstances of the accident
A malfunction occurred on a cup packer during the night shift. The machine operator informed a fitter to rectify the cause. To find the fault, the fitter opened a protective cover on the side of the machine and bridged the associated position switch with a replacement actuator. While the locksmith was inspecting the cause of the fault, he leaned into the danger zone of the machine. At this moment, his head was trapped by the machine’s gripper and he suffered fatal injuries. Following this accident, six employees who were present at the time of the accident suffered post-traumatic stress disorder.
Accident cause
The protective cladding was opened to find the cause of the fault. The position switch was bypassed so that the machine could be operated with the cladding open.
Accident prevention
The accident could have been avoided if suitable protective measures had been taken to eliminate the fault, e.g. the use of an inching mode with enabling switch. The protective cladding that makes sense in normal operation is disruptive for this activity. It is therefore important to evaluate each protective device for each activity in terms of its incentive to tamper.
Arm amputation on a coating machine
Circumstances of the accident
An employee removed a sample from a coating machine during production. The machine had been manipulated in such a way that it could run despite the safety guard being open. This was possible because the holder of the interlock switch of the large front window had been removed.
In the process, the employee lost his right arm in the shearing point between the lower edge of the drum and the reversing bucket.
Accident cause
There were persistent problems with the quality of the coating. The production parameters therefore had to be checked several times during production. In order not to interrupt the process, the employees frequently reached into the open, running machine.
Accident prevention
The accident could have been avoided if sampling had been taken into account during the design phase of the machine and suitable protective measures had been provided. This clearly shows that potential hazards can be reduced if the operator and manufacturer agree on the exact production processes in advance.
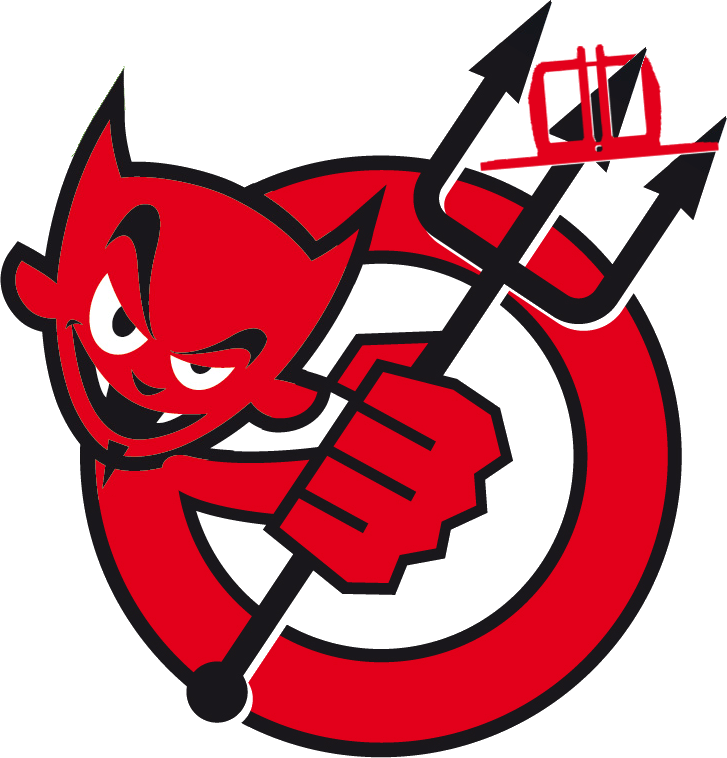