Manufacturer
Safeguards on machinery are seen to be defeated in many companies. Defeating refers to any action by which safeguards are dismantled, bypassed or otherwise rendered ineffective. It often leads to serious accidents, in some cases fatal. Safeguards are defeated by machine operating personnel for a variety reasons: owing to missing operating modes or unfavourable work processes, or to speed up work, to name just three. The machine manufacturer is obliged to reduce the incentive to defeat safeguards and thereby make safe working possible.
Design
The manufacturer’s scope for influencing the likelihood of users defeating safeguards at a later stage begins at the machine’s design stage. The design of the machine must give consideration to the safety concept. Besides increasing safety, this also saves costs, as changing the safety concept at a later stage is usually expensive.
Specifying requirements precisely
In addition to the work tasks to be performed on the machine, the manufacturer must also clarify its intended use with those responsible at the company operating it. The intended use also includes the anticipated working environment and the properties of the material to be processed.
This ensures the machine’s suitability for the intended purpose, and that defeating of safeguards is largely prevented.
Developing the safety concept and machine functionality simultaneously
If the safety concept and the machine’s functionality are planned together, safeguards can be designed such as to present the least possible hindrance to the machine operating personnel.
During planning of the safety concept, all operating modes and all tasks performed on the machine must be taken into account, including commissioning, setup, maintenance, troubleshooting and cleaning of the machine.
Determining the incentive for defeating
Once the safety concept has been developed, the potential incentive for defeating the planned safeguards must be examined. The future machine user can also provide valuable information in this area. Should an incentive exist to defeat safeguards, the design of the machine must be modified.
Construction
The manufacturing company is obliged to comply with the requirements of the EC Machinery Directive (2006/42/EC). The safety concept must prevent safeguards from easily being bypassed or rendered non-operational, i.e. by the use of readily available objects (Annex I, 1.4.1).

Preventing defeating of safeguards
On a machine that presents no incentive to defeat safeguards, the operating and safety concepts are aligned such that the operating personnel do not perceive the safeguards as a hindrance to the work process. Suitable safety concepts and operating modes are in place for all work tasks to be performed on the machine. At the same time, the reliability of the machine supports the avoidance of faults that could provide an additional incentive for safeguards to be defeated.
To prevent the defeating of safeguards effectively, the prioritization of risk reduction measures set out in ISO 12100 must be observed. If risks have already been reduced by design, further protective measures may be unnecessary, as defeating of safeguards in the future is virtually ruled out as a result.
When designing machinery and safeguards, the manufacturer must ensure that ergonomic principles are observed:
- Easy access to maintenance and servicing points
- Clear and unambiguous displays and instruments
- Simple, intuitive operation of controls
- Safeguards permit an adequate view of the work process
During development of the machine control system, it must be ensured that processes are clearly structured and logically sequenced. It must be possible to interrupt production processes, for example for troubleshooting, adjustment of process parameters or quality control. Loss of time and material must be reduced to a minimum. Safe solutions must be put in place for elimination of all foreseeable faults.
Should an incentive to defeat safeguards still exist following implementation of the measures to eliminate it, defeating must be made more difficult, or measures implemented to detect safeguards that have been defeated.
Making defeating of safeguards more difficult
Where a safeguard can be defeated quickly and with little in the way of tools, the risk of it being defeated cannot be ruled out even where the incentive to do so is low.
Interlocks for guards are the safeguards most frequently defeated. ISO 14119 specifies the following measures to prevent such safeguards from being bypassed:
- Preventing access to the elements of the interlocking devices by placing them out of reach, fencing them off or shrouding them, or placing them in a concealed position
- Use of coded actuators to prevent readily available objects being used as substitute actuators on interlocking devices
- Use of non-detachable fastening methods to prevent elements of the interlocking device being removed or repositioned (e.g. welding, bonding, clutch-head screws, rivets)
- Preventing bypassing by means of a bypass monitoring facility in the control system, status monitoring or periodic checks (see “Detecting defeating of safeguards”)
Detecting defeating of safeguards
Where beneficial, safety functions and components should be monitored by the machine control system with regard to both their function and their position in the process sequence. This results in a defeated safeguard being detected in good time by the machine’s control system, enabling appropriate action to be taken.
The following procedures have proved suitable for this purpose:
Status monitoring: The plausibility check detects an unusual sequence of states during a machine cycle. For example, the control system expects a door to be opened at a specific point in the cycle. The absence of the control signal indicates that a safeguard has been defeated.
Periodic checks: The control system prompts the operating personnel to actuate the safeguard. The absence of the anticipated control signal indicates that a safeguard has been defeated.
Measures can be implemented in the control system that respond to detection of a defeated safeguard by making defeating impractical for the operating personnel. Possible implementations:
- Delayed restarting of the process
- Prevention of a process restart
Documentation
The operating instructions must be formulated clearly and structured to enable all relevant content to be found quickly.
The operating instructions must describe how all tasks required on the machine are to be performed safely. This also covers the operating modes and safety measures provided for this purpose, in particular for maintenance and troubleshooting.
Use of technical equipment such as an enabling device or the possible use of inching mode, in particular, should be covered.
The qualifications expected of persons performing tasks on the machine must also be addressed.
To reduce the incentive to defeat safeguards, the operating instructions should include the following information:
- Descriptions of built-in diagnostic systems to support fault detection
- A list of displays for fault identification and localization
- Required tools and materials
- Instructions for starting standby or substitute systems, and for switching off and isolating malfunctioning units
- Information on fault signalling and localization
Should it be found during preparation of the operating instructions that insufficient information is provided on the safe procedure for maintenance or fault clearance, it is urgently recommended that assessment of the incentive to defeat safeguards be repeated.
Sale
Advising customers well and clarifying their needs as precisely as possible before you sell a machine help to ensure that safeguards on machines are not defeated during later operation. The objective is to support the purchaser during the procurement process, so as to provide them with a machine that is ideally suited to their needs.
It is therefore advisable to clarify crucial questions in conjunction with the customer before the sale:
- Clarification of the machine’s suitability
Is it clear, how machine is intended to be used and how it will be used by the customer? Is the machine actually suitable for the intended use, and did the customer specify precise requirements (preferably documented in writing)? - Special operating modes
Experience has shown that performance of work on the machine in special operating modes, for example during setup or tool changing, often gives rise to specific customer requirements. It is therefore essential to clarify whether these requirements, as requested by the customer, can be met with the existing operating modes on the machine, or whether modifications are necessary. - Ease of use
Does the machine’s ergonomics also meet customer requirements, and is it user-friendly? This is particularly important in special operating modes, as customers often require a direct view of the process.
Placing on the market
Assembly and installation are, like operation, setup, cleaning and maintenance, a part of the machine’s life cycle. The manufacturer must therefore design the machine such that these tasks, too, can be performed without safeguards being defeated. The resulting safe working practices protect the manufacturer’s own personnel. At the same time, the defeating of safeguards and setting of a corresponding bad example at the customer’s site, and possibly even assistance by the manufacturer’s personnel in defeating the safeguards, is avoided.
Even where machine manufacturers’ safety concepts are well thought out, they often fail to take account of all the specific requirements and production conditions at the user’s premises. To ensure that all necessary tasks can still be performed easily by users and are compatible with the production process without the need for machine safeguards to be defeated, the manufacturer’s plans must be compared again with the user’s requirements before being accepted. For special machines in particular, it is also advisable to obtain customer approval at the design stage, e.g. between individual design phases. This enables costly subsequent adjustments to be avoided.
Enabling work to be performed in accordance with the user’s requirements and without the need for safeguards to be defeated is of course only the first step; the intended working methods must also be known to all operating personnel. Manufacturers should offer the user training or instruction, provided by themselves or third parties.
Following placing on the market
Once the machine has been placed on the market, the manufacturer is obliged to monitor its use. This means that the product must continue to be monitored for undetected faults and consequences of its use with the potential to cause hazards, and that it should be recalled from the market if necessary (see Machinery Regulation, Article 10 (4)).
How can manufacturers determine whether safeguards on their own machines, at the customer’s premises, are being defeated? This knowledge is usually available to sales and maintenance personnel who are in direct contact with the customer. Operators themselves are another source of information. Should reports have been received of dangerous situations or accidents (including near accidents), these must also be referred to.
Based on these observations, the manufacturer can draw conclusions concerning the machine’s safety concept and consider them during the design of future machines.
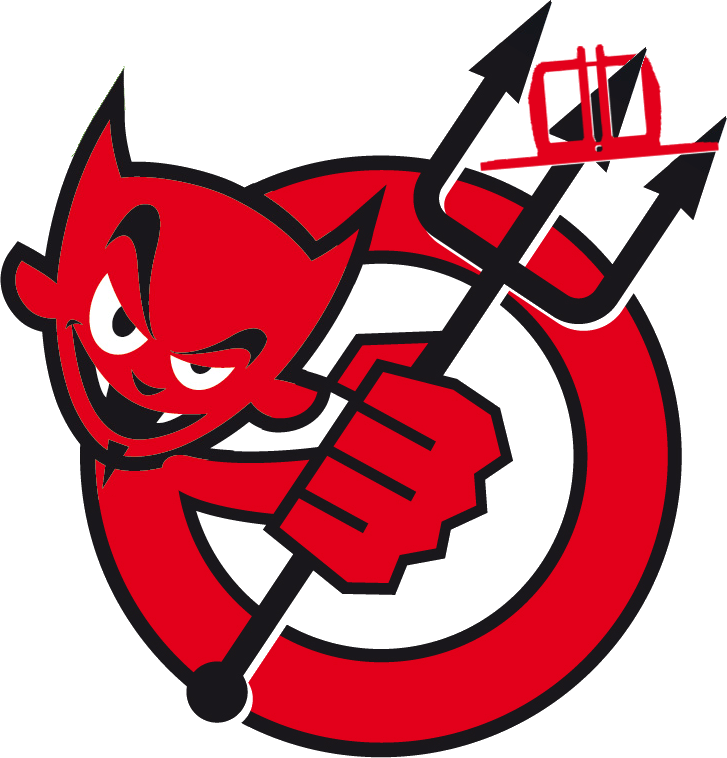