|User|
Operation of machinery
Job safety analysis
Job safety analysis of machines in service should be conducted at regular intervals. An analysis may be prompted for example by information provided by operating personnel, damage to property, malfunctions, or changes in working procedures or the state of the art. The job safety analysis must be updated immediately in the event of:
- Changes in work equipment or working conditions
- New information, e.g. findings from accidents or preventive occupational medical care
- Ineffective or inadequate protective measures
This applies in particular to machines that were placed on the market before the Machinery Directive was adopted and/or for which a conformity assessment was not performed. Such legacy machinery often exhibits a lower safety standard than that required for new machinery. It often lacks dedicated operating modes for manual intervention, as is required for example for setup of the machine; when such a machine is to be set up, defeating of its safeguards is then unavoidable.
Operation and organization
Machines may be operated in the European Economic Area only if their safety level corresponds to the state of the art. This begins at procurement and ends at decommissioning. To ensure that machines remain safe throughout their life, the user must take measures extending beyond mere technical maintenance.
Instruction as a measure for raising risk awareness
Machinery is continually becoming safer. However, the numerous safeguards may lead to a false sense of security. The assumed higher level of safety encourages employees to take greater risks. In particular, when employees are not aware that the safeguards have the purpose of making execution of work processes safe, they perceive them as a hindrance, resulting in an increase in risky behaviour and thus also in the incentive to defeat the safeguards.
Periodic instruction of employees not only expands knowledge and imparts skills, but can also create, change, reinforce and establish attitudes. At the same time, instructors should be motivated to behave safely themselves and thereby set an example to employees.
Whether employees actually behave as was instructed, practised and agreed during instruction often becomes apparent only in practice. The supervisor must therefore also monitor this behaviour. Once inappropriate behaviour has become the norm, it often cannot be prevented by a single instruction measure. Supervisors must therefore be patient, whilst at the same time rigorously putting a stop to behaviour that contravenes safety and health.
Organization of checks on safeguards’ effectiveness
In their job safety analysis, the employer must specify the form and scope of the tests required for each item of work equipment. These include checks on the serviceability of safeguards. In addition to information in the manufacturer’s operating instructions, the current incidence of defeating of safeguards in the company must also be taken into account when the inspection intervals are specified.
Regular visual inspection is sufficient to detect many defeated safeguards. The following are indicative of defeating:
- Actuators of interlocks that have been detached from the guard and remain permanently plugged
- Drilled-out screws or empty holes for fixings indicating where safeguards have been removed
- Screws on which the tamper-proof paint has been scratched off, indicating where a safeguard has been removed
- Spare actuators lying around at the workstation or carried by employees (e.g. maintenance staff): this indicates that defeating occurs regularly, or at least that these employees are setting a poor example
If a defeated safeguard is detected during the visual inspection, defeating must be reversed, documented and discussed immediately with the manager. In larger companies, the OSH committee meeting is a suitable venue for this purpose.
Regular visual inspections must be conducted or organized by the manager responsible. Support with the inspection can be provided by the OSH professional, or by safety delegates where present in the department.
The visual inspection is supplemented by a functional test of the safeguards. In contrast to visual inspections, which can be performed without intervention in the running process, a functional test must be planned in advance. Regular maintenance activity presents a suitable opportunity in this case. Functional tests may be performed only by trained and instructed employees. Organization of the tests is the responsibility of the manager.
Leadership responsibility
Superiors are responsible not only for the business success of their company, but also, and more importantly, for employees’ safety and health. The standard and efficacy of occupational safety and health depends very much on the attitude, willingness to act and specific action (or lack of action) on the part of superiors and senior management.
According to a recent representative survey (available here), companies in which defeating of safeguards is tolerated by superiors, even if only sporadically, exhibit the following compared to other companies:
- A 50% increase in the defeating of safeguards
- A 100% increase in the incidence of accidents caused by the defeating of safeguards
The primary elements of leadership responsibility for occupational safety and health can be summarized as follows:
- Selection:
Managers must charge suitable and adequately qualified persons with the tasks. Employees who ignore safety instructions or defeat safeguards can be considered insufficiently qualified. - Organization:
Managers are responsible for the safety of work processes. They should ensure that all employees receive regular training and understand the importance of the safety rules in force. This includes, in particular, the preparation of operating procedures and the instruction of employees. - Monitoring:
Managers must take suitable measures to monitor implementation of the measures they have instigated, and must check whether they are sufficient. They must object to any misconduct on the part of employees, rectify unsafe conditions and – if necessary – halt dangerous work.
For effective prevention of the defeating of safeguards, a non-accusatory corporate culture is required that enables employees to draw attention to dangerous behaviour and operating conditions without fear of adverse consequences. Incentives for the defeating of safeguards can thus be eliminated systematically.
Managers should ask themselves the following questions:
- When senior management makes investment decisions, is sufficient attention paid to machine safety?
- Do managers pay attention at procurement to the required safety features/equipment of machinery?
- Is the manager available to take decisions in the event of defects or malfunctions on machinery?
- Do OSH professionals or superiors tolerate unsafe work?
- Are the supposedly good reasons for the defeating of safeguards (work is faster, better, no production stoppage, etc.) recorded systematically, discussed without reproach and eliminated?
- Do maintenance personnel and planning engineers prepare work and maintenance procedures that enable the work to be carried out safely?
- Are employees permitted to interrupt tasks that are not safe in order to rectify deficiencies, without fear of adverse consequences for themselves?
- Do the operating personnel and OSH professionals have access to straightforward communication channels to raise deficiencies, faults, and hazardous activities they have observed?
- Are they heard without reproach and given priority?
- When the defeating of safeguards is observed, is the response not “Who did this”, but “How can we change this”?
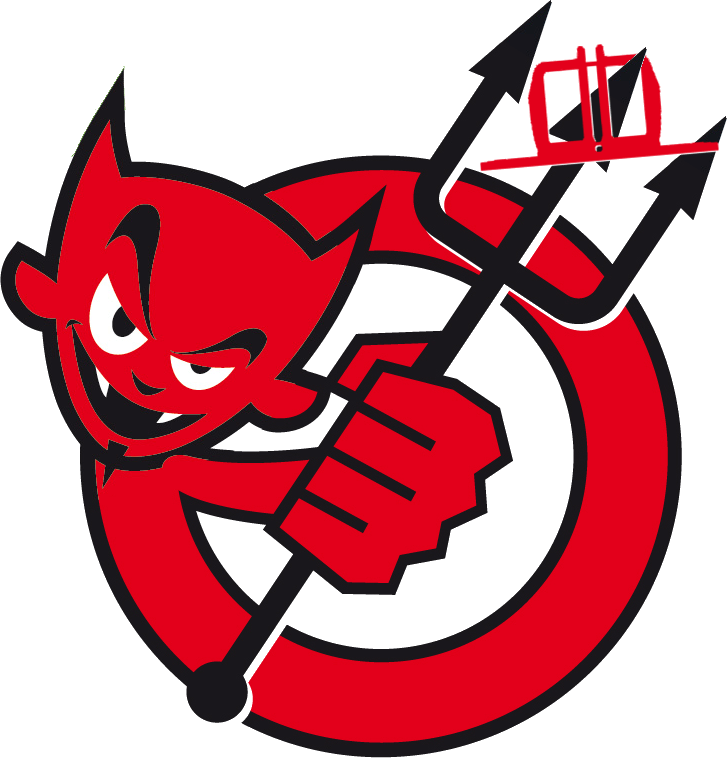